Het onmogelijke mogelijk maken – Fieldman
3D-printen omarmd
Peter Veltman is een soort Willie Wortel. Wat zijn ogen zien, zetten zijn hersens om in een geautomatiseerde verbetering en verzorgt hij tot in de puntjes. Hij gaat pas weg als het werkt. En waar het kan, gebruikt hij 3D-geprinte onderdelen.
Of, zoals hij zelf op zijn LinkedIn pagina zegt: Door out-of-the-box denken kom ik met mogelijke oplossingen voor ‘onmogelijke problemen’. Het gaat mij daarbij om het totaaltraject: van innovatief idee, via technisch en functioneel ontwerp, naar realisatie en implementatie. Dat maakt nieuwsgierig, dus togen we naar zijn kantoor in een prachtig Koetshuis in de Betuwe om hem aan de tand te voelen.
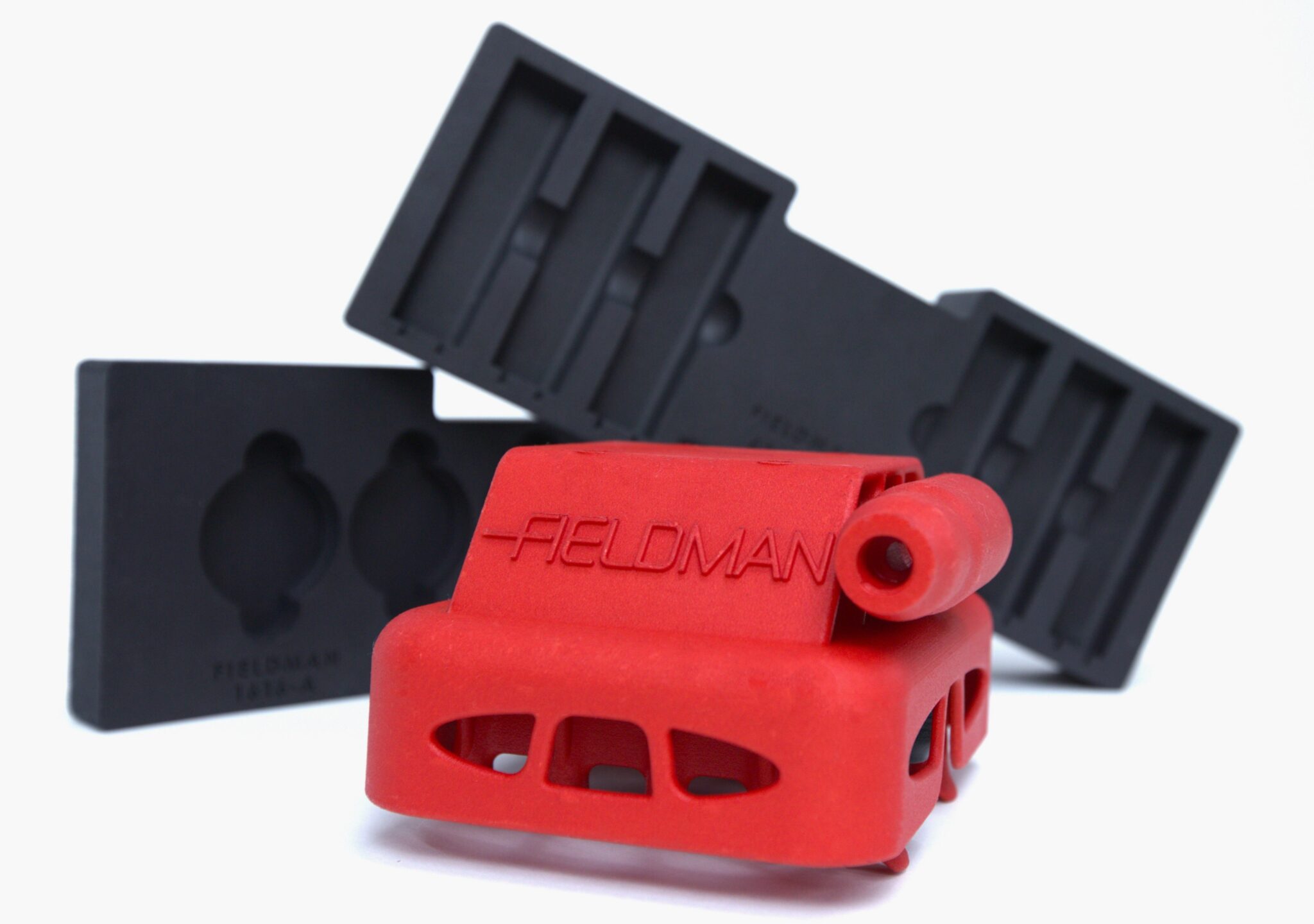
Inhoudsopgave
Dat kan slimmer
“Ik begon ooit met werken in een etikettendrukkerij. Daar heb ik veel geleerd over etiketten en de uitdagingen waar je mee te maken krijgt bij het etiketteren van producten en verpakkingen. Vanuit die drukkerij ben ik voor mezelf begonnen in de handel van etiketten en de machines die bij het etiketteren komen kijken. En van lieverlee kwam ik steeds meer tot de ontdekking dat dingen slimmer konden. Als iemand zei dat iets niet kon, wilde ik kijken of er toch niet een mogelijkheid was. Ik zeg ook wel: Ik begin waar een ander het heeft opgegeven”, hij lacht breeduit.
Vanaf het moment dat 3D-printen in beeld kwam, werd hij enthousiast. Via een simpele zoekopdracht op Google landde hij bij Parts On Demand, dat ook nog eens vlakbij gevestigd bleek te zijn. “Met Neil van Es had ik direct een klik, we denken allebei sneller dan we praten en het is heel prettig als je met iemand kunt schakelen die direct weet wat je bedoelt.” Hij vond het daarom best lastig toen Parts On Demand hard groeide en Neil op een gegeven moment vertelde dat hij collega Anne van den Dool naar voren wilde schuiven. “Ik had daar best wel een hard hoofd in, want als je iemand hebt gevonden waar je zo goed mee kunt samenwerken, dan is het lastig om te geloven dat dat met een ander ook lukt. Maar ik moet zeggen, Anne heeft mij verrast en verbaasd.”
Hoge variatie
Zo bedacht hij een mechanisme om kratten open te klappen voor een invoerlijn. Het type kratten bleek verschillende variaties te hebben. “Mijn klant kwam steeds weer met een nieuw type krat aan dat nog niet in de vraag was meegenomen. Op een gegeven moment kwam er zelfs een krat waarvan de wanden niet zomaar opvallen als je hem op zijn kop houdt. En de snelheid moest er natuurlijk ook inblijven, vier per seconde alstublieft. Dus moest daar een mechanisme voor ontwikkeld worden dat de kratten geforceerd open zou vouwen. Dat mechanisme had ik bedacht en Anne had het 3D-printwerk van het hulpstuk uitgevoerd. En ze was me zelfs al een stap voor met de uitvoering! En dat is precies wat ik nodig heb. Met een meeprater kan ik niets, iemand moet mij wel tegengas kunnen geven en de techniek van het 3D-printen vraagt echt om heel anders te denken over het ontwerp van je onderdeel. De buitengewone mogelijkheden die het geeft, vragen om alles los te laten wat je in 2D-ontwerpen deed.” En dat gaat Veltman prima af, op een kladblok tekent hij een machine: “Je moet een ruimtelijk inzicht hebben als je ontwerpt.”
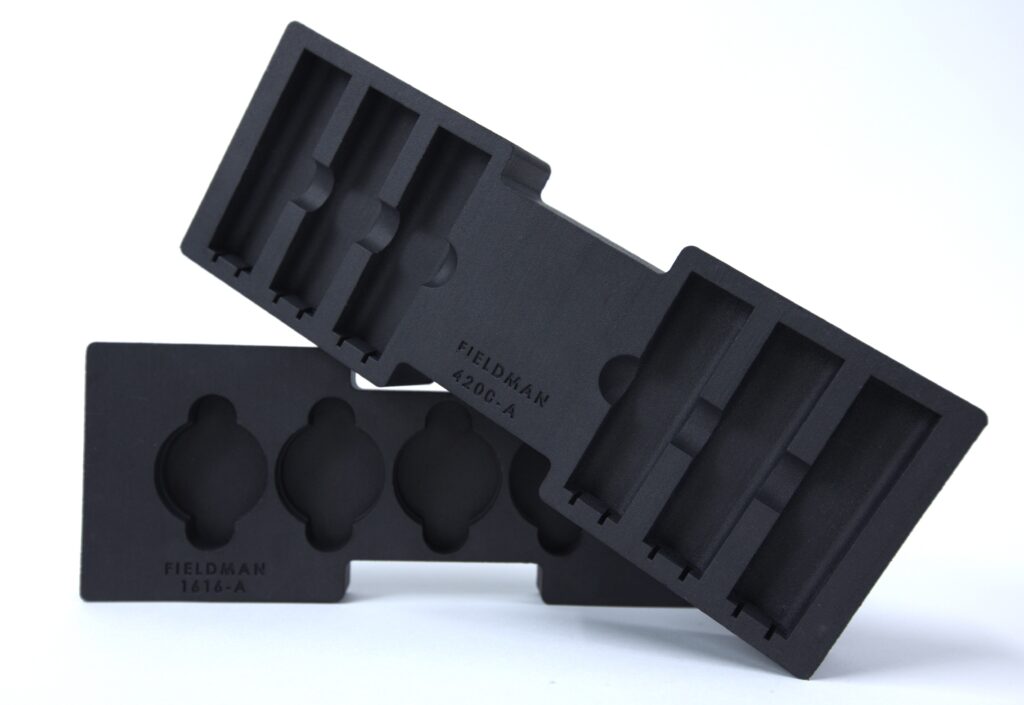
Ontnesten
In een ander project in een invoerlijn worden fruitbakjes geautomatiseerd ontnest en in een krat geplaatst. “Ik kwam bij een klant voor een etiketteermachine. Daar zag ik deze handeling handmatig gedaan worden. Heel veel medewerkers die in hoog tempo bakjes van een stapel haalden en ze vervolgens in een krat plaatsten. Toen ik die klant vroeg waarom hij in vredesnaam die mensen dat saaie werk liet doen, kreeg ik als reactie dat als ik dat kon automatiseren, dat ik het dan maar moest laten zien. Nou, dat heeft ie geweten!” Hij haalt zijn telefoon tevoorschijn en laat een video zien waar inderdaad deze handeling volledig geautomatiseerd gedaan wordt. En met een tempo dat je duizelt! Met schroefontnesters en geavanceerde grijpers op een robotarm worden bakjes in een razend tempo in kratten geplaatst die via een invoerlijn het vul- en weegproces in gaan. “Ik word zelf gewoon bang van die machine, het is echt een beest!” zegt hij met volle overtuiging. Maar als je de capaciteit van die machine hoort, 12.000 bakjes per uur, dan kun je je daar iets bij voorstellen.
Veel 3D-printen
Alles wat te maken heeft met weeg-, prijs- en etiketteerhandelingen heeft zijn aandacht. “Ik ontwikkel en bouw als een van de weinigen in Europa alles zelf, altijd op maat en met de kwaliteit van een Rolls Royce. Sommige onderdelen werden gefreesd, gelaserd of gevouwen en ik kreeg eigenlijk wel een beetje genoeg van die handelingen en de bijbehorende kosten. Ik ben toen gaan snuffelen aan de mogelijkheden van het 3D-printen. Ik begon met één onderdeel en vervolgens nog een onderdeel en zag er de functionaliteit van in. Ik wilde een van de eersten zijn met het toepassen van zoveel mogelijk 3D-geprinte delen, maar die moeten wel een hoge kwaliteit hebben. Ik ben al bijna vanaf het begin van Parts On Demand klant, het is heel prettig als je twee techneuten hebt die elkaar snappen en aan een half woord genoeg hebben.”
Al zijn ideeën ontstaan in de praktijk, soms door het uit zijn ooghoeken spotten van een detail. “Dat gaat dan in mijn hoofd zitten en komt er dan even later uit als een oplossing voor een probleem. Out-of-the-krat, zou je kunnen zeggen. Want je haalt je inspiratie natuurlijk soms uit de gekste dingen.” Hij haalt nogmaals zijn telefoon erbij en laat een paar video’s zien van testen en hoe het proces verloopt van een vraag naar een idee naar testen tot ontwikkelen en inbedrijfstellen. “Kijk bij deze test zie je hier in beeld een lagerblok: geprint natuurlijk – want dat is heel eenvoudig te printen, dat was een van de eerste dingen die ik met 3D-printen deed.” We zien hoe zijn idee gaat van proberen tot verbeteren tot een nieuwe vraag tot verder verbeteren.
Capaciteit verhogen
Op een kast zien we een geprint ventieleiland liggen. Op de vraag waar hij die voor gebruikt, haalt hij wat vormdelen tevoorschijn en vertelt hij over hoe hij aan de praat raakte met een grote relatiegeschenkenleverancier. Die wilde zijn productie verhogen, maar had nog een redelijk lage automatiseringsgraad in het bedrukken en verpakken. “Toen ik vertelde wat ik voor capaciteit zou kunnen realiseren, was de zaak snel beklonken. Met als kernproces het digitaal bedrukken van die geschenken. Pennen worden met dit ventieleiland als vacuümgrijper opgepakt en gepositioneerd op shuttles met mallen en getransporteerd. En zoals altijd, is de flexibiliteit van de oplossing hoog. Want de variatie in de vorm van de pennen, maar sowieso van de bedrukte producten is hoog. En een automatiseringsoplossing is pas ideaal als je veel variatie aankunt. Dus dat is altijd een belangrijk onderdeel van de oplossing.” Voor deze toepassing werd een mal met twee verschillende materialen geprint, in een combinatie met het TPU.