Samen kom je verder – AIM
Specialisten vinden elkaar
In het Limburgse Brunssum stappen we het gloedjenieuwe deel van het bedrijfspand van AIM binnen. In de net gerealiseerde uitbreiding ontmoeten we Leon Habets en Mathijs Franssen die ons uit de doeken doen wát hier allemaal voor spannends wordt geproduceerd en wat Parts On Demand daarmee van doen heeft.
AIM B.V. is een onafhankelijke productiepartner voor elektromechanische apparaten voor de medische- én life-science-sector. Leon is senior engineer en Mathijs heeft op zijn visitekaartje de functie Initial Purchaser staan. Door de geschiedenis van het bedrijf is een bijzondere mix van werkzaamheden ontstaan. “We begonnen ooit als een werkvoorziening na het sluiten van de mijnen. Onze fabriek vervaardigde fysioapparatuur voor Enraf Nonius, wat later een onderdeel van Delft Instruments werd. Het bedrijf werd verzelfstandigd en kreeg de naam AIM, wat staat voor Advanced Instruments Manufacturing. En die afkorting dekt niet alleen precies de lading, maar past ook nog eens in het logo dat vervangen moest worden.”
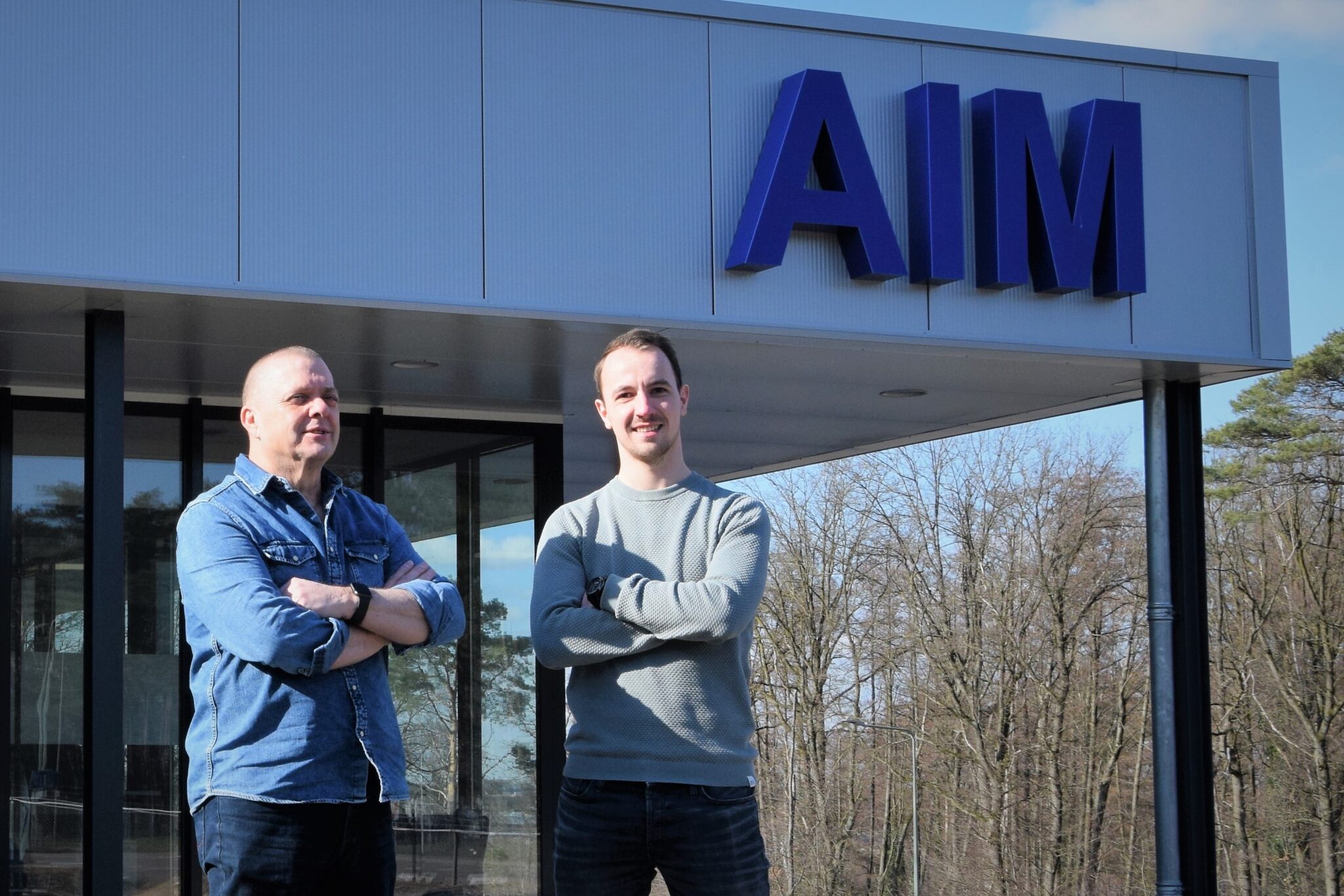
Inhoudsopgave
Gewilde combinatie
Voor die werkzaamheden is AIM in het bezit van een reeks certificeringen voor het produceren van apparaten voor de medische sector en lifescience industrie. En laat dat nou een gewilde combinatie vormen met de kennis, ervaring en productiecapaciteit. “Voor een klant uit Eindhoven produceren we een geavanceerd laboratoriumapparaat. Daarvan maken we nu de vierde versie waarbij het aankomt op nauwkeurigheid”, vertelt Leon. “Onder cryogene omstandigheden worden laboratoriummonsters in grids van 3 millimeter doorsnede met 100 gaatjes ingevroren met vloeibaar stikstof bij een temperatuur van -160 graden Celsius, dat vraagt wel iets van de constructie.”
Er passeren flink wat medische toepassingen de revue tijdens het gesprek. Zo worden er blowers voor warmtedekens voor in de operatiekamers gemaakt, maar ook apparaten waarin het verwarmen van bloed plaatsvindt. Voor fysiotoepassingen zijn er fietsen, loopbanden en crosswalkers, de wat gangbaardere oefenapparatuur. Maar ook hoogfrequente behandelapparatuur komt uit deze werkplaats.
Ideale partner
“Door onze ervaring in al deze sectoren zijn we ook een ideale partner voor startups in de zorgsector. En wordt momenteel enorm veel nieuwe technologie toegepast in innovatieve producten en we werken graag mee om de productie daarvan marktrijp te maken”, vertelt Mathijs. “Soms gaat het alleen om het echte produceren en staat het volledige design al vast. Soms komen we in overleg met de klant tot verbeteringen. Zo werken we op dit moment samen met een startup die desinfectie op basis van uv toepast in allerlei vormen, bijvoorbeeld voor het ontsmetten van smartphones. In de coronaperiode kwam deze behoefte ineens sterk opzetten.” Een andere startup zullen we binnenkort ook eens gaan bezoeken voor een verhaal, het gaat om Elitac, daar worden Balancebelts gemaakt voor mensen met een evenwichtsstoornis. En ook daar mag Parts On Demand een bijdrage aan leveren. Leon: “Een ander project waar we voor een klant aan werken is een geavanceerde rolstoelbesturing die met beweging van het hoofd of voeten, of een combinatie hiervan, zorgt voor de gewenste stuuropdracht. Waarmee de rolstoelinzittende een grotere onafhankelijkheid behoudt. Deze besturing kun je dus heel specifiek op een client aanpassen in combinatie met de rolstoel. Tja, partijen benaderen ons omdat we gecertificeerd zijn en over de faciliteiten beschikken.”
3D-printen
“Als het onderdeel een complex design heeft en ook nog in relatief kleine series vervaardigd moet worden, dan is spuitgieten niet interessant. Klant Elitac had precies zo een behoefte en zelf al contact met een 3D-printbedrijf: Parts On Demand. Wij hadden eigenlijk geen ervaring met 3D-printen en Parts On Demand is inmiddels voor ons de go-to-partij geworden, en niet alleen omdat zij ook de juiste certificering hebben. Inmiddels zijn we al een tweede project met hen aangegaan, de SPAT. Ook daar is sprake van complexe onderdelen en deze kún je zelfs niet eens spuitgieten. We hebben hiervoor Ron Verleun van Parts On Demand benaderd met de vraag: hoe gaan we dit aanpakken”, vervolgt Leon.
Voor dit project zijn sets van enkele tientallen onderdelen nodig met gespecificeerde materialen en toleranties. “We zijn een hele dag bij Parts On Demand op bezoek geweest met een van onze engineers. Elitac was zo enthousiast over het bedrijf dat we dat ook graag met eigen ogen wilden zien. We hebben een eerste batch onderdelen als test laten maken om de kwaliteit te kunnen beoordelen en kleurproeven mee te doen. Ze hebben de specialistische kennis, ervaring, cases en certificering die wij nodig hebben om er een goed gevoel over te hebben. Dat is echt fijn!”
“Ze zijn vervolgens ook hier op bezoek geweest, en op hun beurt willen ze ons weer betrekken bij projecten. Het is een hele fijne relatie, ze zoeken echt de samenwerking, ook tussen klanten onderling. De cultuur van het bedrijf, de missie en de visie, het past heel goed bij wat wij voor ogen hebben.”
De SPAT
Wat is de SPAT dan precies is, dat willen we natuurlijk ook wel even weten. Leon legt uit: “Het is een apparaat dat automatisch allergietesten kan uitvoeren. Het apparaat kan met 12 lancetten – pennetjes met twee scherpe puntjes – kleine krasjes op de arm maken. Er wordt direct met het krasje een allergeen opgebracht en de bediener kan vooraf in een menu automatisch registreren voor welke allergenen er getest wordt. Na een kwartier beoordeelt een arts het resultaat en de test gegevens worden volledig geregistreerd en zijn opvraagbaar op het apparaat. Met de traditionele techniek gaat dit over veel meer schijven, zijn er meer mensen voor nodig en kost het veel meer tijd. Nu kan het zonder lab en is iedereen sneller klaar, inclusief de patiënt.”
De SPAT, oftewel Skin Prick Automated Test – het idee van een arts die het vervolgens samen met een universiteit tot een volwaardig product heeft bedacht. Het aantal gebruikte lancetten is afhankelijk van de te testen allergieën. Leon legt uit dat de arts de interpretatie van de resultaten doet en de uitslag geeft. “De data wordt op het scherm weergegeven, dus het lijkt best waarschijnlijk dat je in de toekomst de uitslag ook van de apparaat krijgt. De eerste SPAT wordt binnenkort door AIM geproduceerd en de verwachting is dat deze in veel ziekenhuizen en huisartsenpraktijken snel geplaatst zullen worden.”
Steeds sneller
“De technologie gaat zich steeds sneller ontwikkelen. Dingen die vroeger lastig waren, zijn nu veel makkelijker te realiseren voor een ontwikkelaar. Met behulp van een CAD-systeem kan een ontwikkelaar zo ver doordenken dat het weer lastig te produceren wordt”, lacht Mathijs. “Parts On Demand voegt voor ons kennis en kunde toe, zowel over het proces van 3D-printen als over de materialen en het gedrag daarvan bij deze processen. Denk aan de maakbaarheid, de maatvastheid maar ook de beste printrichting voor de cruciale afmetingen en vormen. Ze maken echt de vertaalslag van metaal naar kunststof.”
Tijdens de rondleiding die we maar al te graag accepteren, zien we dat er wordt gewerkt in productiecellen. Mathijs: “Vroeger deden we echt alles zelf in eigen huis. Plaatwerk, zeten, spuiten, draaien, frezen, en zelfs printplaten bestukken en kabelbomen samenstellen. Dat hebben we gefaseerd uitbesteed, inclusief de mensen en de machines. Nu houden we ons bezig met assemblage, inkoop, verzenden en natuurlijk service en het trainen van de gebruikers service engineers.” In een prachtige omgeving en een mooi nieuw pand!