Hoe diverser, hoe handiger
Variatie? Kom maar op!
Vandaag brengt onze klantenexpeditie ons naar een ziekenhuis. Het UMC Utrecht om precies te zijn. Daar vertellen Thijs Dijkgraaf en Froukje Euwe ons over hun project waarmee ze de efficiënte inzet van beschikbare medische apparatuur weten te optimaliseren. Met behulp van 3D-geprinte hulpstukken.
Froukje Euwe en Thijs Dijkgraaf zijn werkzaam als respectievelijk ontwerper en klinisch informaticus binnen de afdeling Medische Technologie & Klinische Fysica. Met behulp van 3D-geprinte onderdelen hebben ze een systeem ontwikkeld en geïmplementeerd waarmee alles van infuuspompen tot rolstoelen in het ziekenhuis getraceerd kan worden.
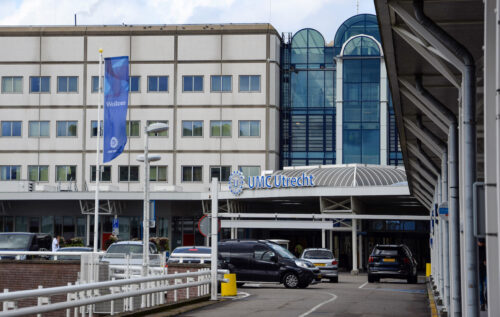
Inhoudsopgave
“De diversiteit van de hulpmiddelen maakt dat we heel veel verschillende oplossingen moesten bedenken om de benodigde trackers veilig en goed te bevestigen. Op infuuspalen, bijvoorbeeld, bleek de bevestiging die we in eerste instantie bedachten, heel kwetsbaar”, vertelt Thijs.
De uitdaging
Even kort over de problematiek: Iedere afdeling in een ziekenhuis beschikt over medische hulpmiddelen. Soms zijn de aantallen van een hulpmiddel gebaseerd op het type zorg dat die specifieke afdeling biedt, soms is er ad hoc iets nodig. Hulpmiddelen worden verplaatst over verschillende afdelingen, waardoor het overzicht snel kwijt is.
Bijvoorbeeld die infuuspomp die met een patiënt mee verhuist naar een andere afdeling. Of je het nu hebt over rolstoelen, meetapparatuur, of voedingssondes, voor ieder hulpmiddel geldt dat het fijn is als je weet waar het zich op enig moment bevindt. Is het inzetbaar of in gebruik, én dat je inzicht hebt in de status van het onderhoud.
En laat de moderne technologie daar nou prachtige oplossingen voor bieden! Track & trace is inmiddels een alledaags begrip. Maar hoe is die infuuspomp te tracken? Om het track & trace principe praktisch werkbaar te maken in een ziekenhuis, dat was de uitdaging. Het trackingsysteem dat in het UMC Utrecht is gekozen werkt op basis van een Wirepas meshnetwerk. Dat betekent dat er overal zogenaamde ‘nodes’ of knooppunten met elkaar communiceren. Deze Finse technologie zorgt voor schaalbaarheid die vele duizenden sensoren kan verbinden.
Meerwaarde
“Dit project heeft een lange aanloop gekend. In een vooronderzoek hebben we de verschillende beschikbare technieken bekeken en ook intern op twee afdelingen pilots gedraaid. Je kunt wel academisch bedenken dat er anders met hulpmiddelen omgegaan moet worden, maar hoe werkt het in de praktijk?” Thijs vertelt over de interactie met het personeel: “We kregen hele waardevolle informatie die we vervolgens konden vertalen in uitgangspunten voor het project. Zo bleken de taghouders heel belangrijk. Ze moesten de functionaliteit niet belemmeren en de uitwerking bleek voor de medewerkers ook echt iets op te leveren. Dat blijkt in de praktijk ook echt zo uit te werken: in plaats van bezig te zijn met de apparatuur, kunnen ze die tijd nu besteden aan de patiënten. Iedere afdeling was voorheen namelijk zelf verantwoordelijk voor hun eigen apparatuur. Niet alleen het bijhouden waar alles zich bevond, maar ook het tijdig onderhoud laten plegen. Een belangrijke vraag die we in deze pilots onderzochten was welke positienauwkeurigheid er nodig is.”
Onderzoek
Thijs vertelt dat er een heus Experience Center werd ingericht samen met de industrie. “We konden zo heel goed definiëren voor welk probleem we welke oplossing zochten. Uiteindelijk hebben we besloten om de Wirepas-technologie te gebruiken in combinatie met de trackers van Fujitsu en en de systematic Collumna Flow software om de locatiedata aan de zorgprofessionals ter beschikking te stellen.”
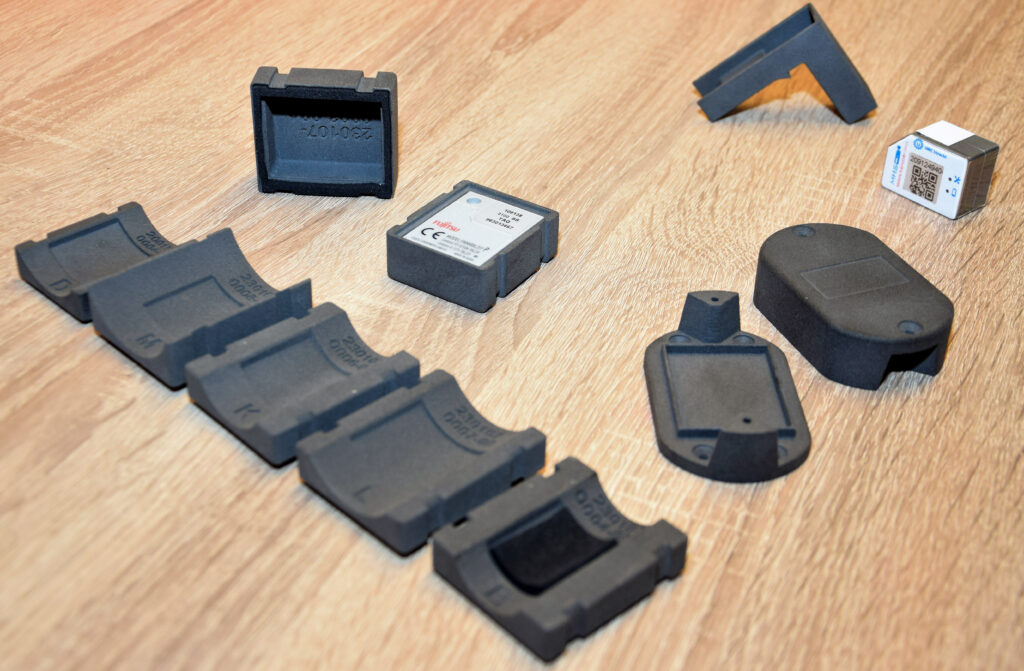
Gouden resultaat
We hebben nu de informatie over locatie en onderhoud per hulpmiddel inzichtelijk. Dat heeft een enorme tijdsbesparing en efficiëntieverbetering opgeleverd. De hulpmiddelen worden centraal beheerd, gereinigd en onderhouden en kunnen vraaggestuurd naar de afdelingen gebracht. En dankzij de veel hogere efficiëntie van de inzet, is er een veel grotere wendbaarheid van de inzet gekomen. Iedereen kan zich bezighouden met zijn kerntaak, dat alleen al is goud waard.” De volgende stap is dan ook het uitrollen naar andere apparatuur.
Taghouders
Voor de taghouders was dus veel aandacht nodig. Thijs en Froukje tonen een aantal hulpmiddelen en de uitdagingen die ieder van deze middelen met zich meebracht als het gaat om het duurzaam en veilig bevestigen van een tag. “We kwamen al snel uit bij 3D-printen als productietechniek voor de taghouders”, vertelt Froukje. “We hebben zelf een een SLA (vloeistof) printer en FDM (draad) printers staan, dus kunnen voor maatvoering, toleranties en functionaliteit onze eigen proefprints maken. We gebruiken het 3D-printen als techniek al heel lang hier in het ziekenhuis. Kleine aantallen of proefmodellen printen we nog steeds zelf, maar voor grote aantallen zijn we bij Parts On Demand uitgekomen. Eerst hebben we de kapjes voor de transmitternodes van het meshnetwerk laten printen, daarna zijn we met de taghouders aan de slag gegaan. We hebben verschillende materialen getest en we gebruiken nu PA12 als materiaal en zijn heel blij dat dat ook een echt duurzaam materiaal is.”
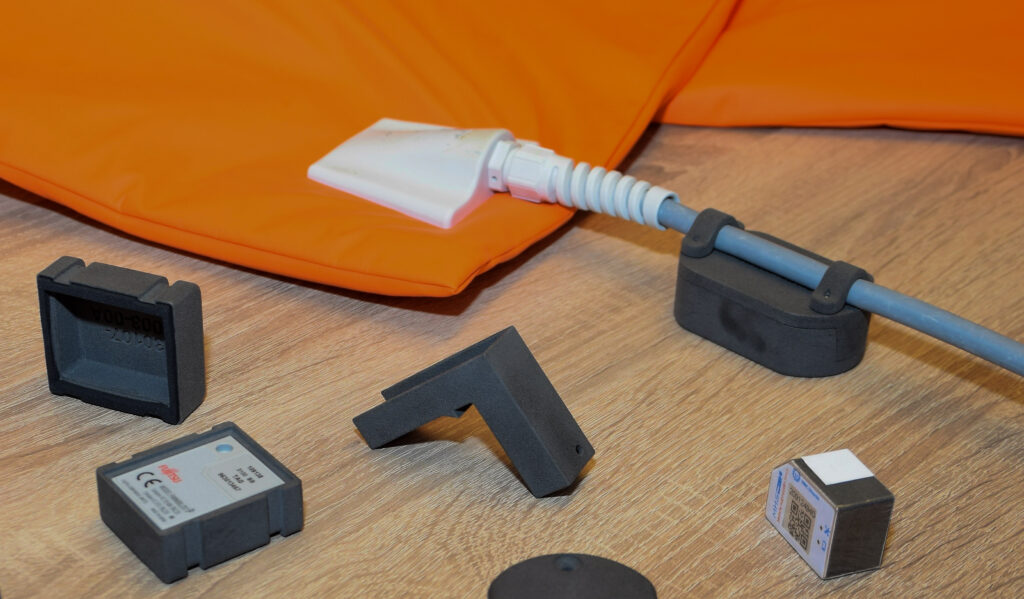
Informatie
Statusinformatie is de ‘heilige graal’, vertelt Thijs. “De informatie die we nodig hebben krijgen we natuurlijk alleen door met de hulpmiddelen te communiceren. We moeten weten waar ieder middel zich bevindt. Door de enorme diversiteit van de hulpmiddelen zijn tags een uitdaging. Dankzij een combinatie van een standaard tag en een 3D-geprinte bevestigingsconstructie kunnen we nu alle hulpmiddelen volgen en hun locatie achterhalen. In sommige gevallen is dit behoorlijk lastig.” Froukje laat een verwarmingsdeken zien die gebruikt wordt in de operatiekamers. Ze legt uit dat het een uitdaging was om een geschikte bevestiging te vinden die niet kwetsbaar is, goed blijft zitten en de functie van de deken niet belemmert.
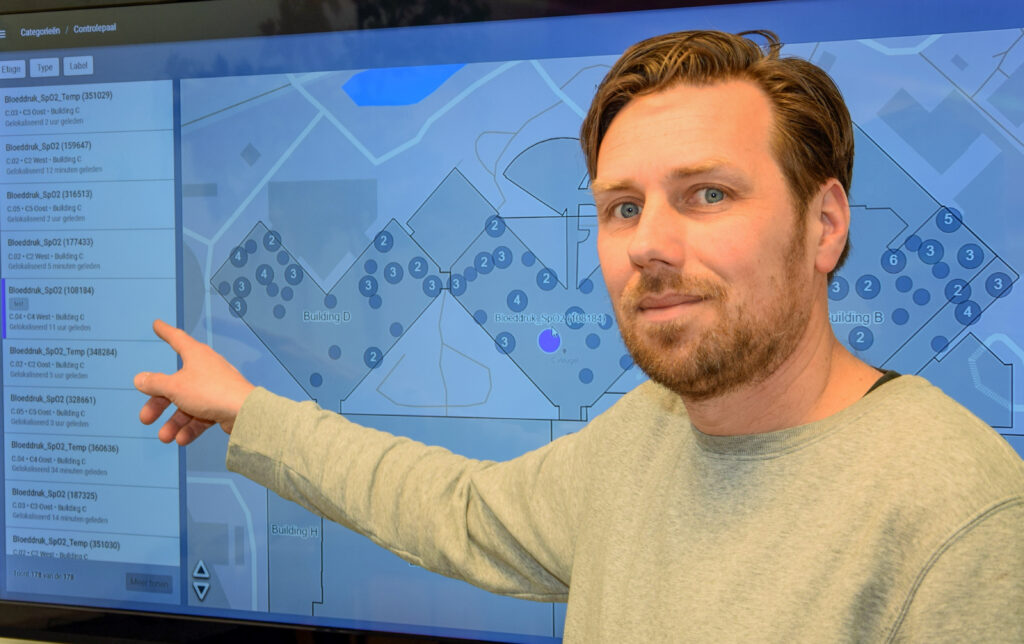
“Ziekenhuizen delen veel informatie met elkaar over hoe ze omgaan met dit soort uitdagingen. We hebben bijvoorbeeld voor de inrichting van de Medische Hulpmiddelen Service goed gekeken naar de serviceafdeling in het UMC in Groningen. Het Experience Center dat we voor dit project hebben opgezet, hebben we ook andere ziekenhuizen uitgenodigd om kennis en ideeën uit te wisselen. We zien elkaar niet als concurrenten, maar helpen elkaar juist verder. We willen graag op dezelfde manier samenwerken met onze leveranciers, en dat is ook wat Parts On Demand belangrijk vindt.”