Beperkingen? Nee hoor.
In de titel van dit artikel ligt het hele verhaal opgesloten. We spreken met Bart de Kiefte, CTO van Livit in Dordrecht waar hulpmiddelen worden gemaakt. Met name op het gebied van protheses, ortheses en braces, maar ook steunzolen, aangepaste schoenen tot steunkousen en veiligheidsschoenen.
Bart de Kiefte van Livit
Op hun website lezen we: “Bij Livit vinden wij dat iedereen het verdient om vrij te kunnen bewegen.” En de klantreacties liegen er niet om, voor dat doel doen ze heel veel. Zo ook op het gebied van ontwikkeling. Parts on Demand mag daar tegenwoordig een bescheiden bijdrage aan leveren.
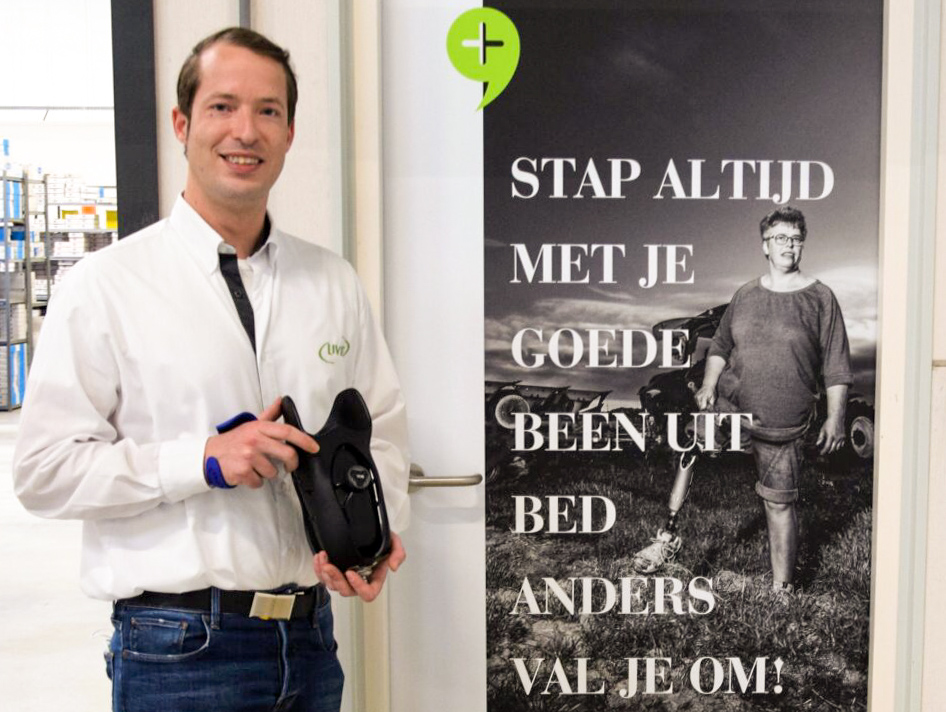
Inhoudsopgave
Automatiseren
In 2012 kwam Bart bij Livit terecht. Hij zag daar een werkomgeving waar hij zich al snel thuis voelde en zijn ei kwijt kon in het automatiseren van zowel de productie als de ontwerpafdeling. “Een half jaar nadat ik in dienst kwam heb ik de CAD/CAM-afdeling opgezet. En in 2014 heb ik een businesscase gemaakt voor robotisering. Inmiddels hebben we er twee in bedrijf, en die hebben zich in een half jaar tot een jaar terugverdiend. Veel stappen in het productieproces zijn herhalingen en dat kun je in een digitaal systeem veel makkelijker inregelen. In het verleden werd alles met gips gedaan, maar met robots gaat dat veel beter en kun je bovendien een betere kwaliteit bereiken.”
De eerste tijd bij Livit bleek een echte eye-opener voor De Kiefte. “Ik dacht bij orthopedie aan steunzolen en braces, maar daar bleek een wereld achter schuil te gaan. Alleen al de enorme hoeveelheid productgroepen geeft een indicatie van de diversiteit. En bijvoorbeeld bij protheses en ortheses krijg je vaak dat die iedere twee jaar vernieuwd moeten worden. Ik heb wel geleerd dat mensen zich vaak tekort doen doordat ze niet aan hulpmiddelen denken. Iemand die moeilijk loopt door een spierziekte bijvoorbeeld, kan met onze Blue Rockers – een dynamische enkel/voet-orthese – veel beter lopen terwijl het niet zichtbaar is voor de buitenwereld.”
3D-printen
Naast het automatiseringsproces heeft Bart ook voorbereidingen getroffen om 3D-printen te introduceren in het productieproces. “We hebben alle afdelingen van de engineering daarbij betrokken, zowel de biomechanische als de industriële en mechanische designers hebben een bijdrage in het geheel. Met het complete engineeringteam hebben we de ontwikkelingen opgepakt en bespreken we wekelijks de voortgang, bijvoorbeeld over de macro’s die gebouwd moesten worden.”
Ook dit pakte Bart al in 2014 op. “We wilden heel goed in kaart brengen wat haalbaar is en wat er precies kan met welke techniek. Neil van Es van Parts on Demand snapt dat heel goed. Samen hebben we de risico’s van de technieken in kaart gebracht en hij heeft ook meegepraat in een panel. Ook robotisering kent natuurlijk risico’s die we uitgebreid hebben overwogen, bijvoorbeeld als het gaat over de werkgelegenheid. Maar de praktijk is dat we sinds de komst van de robots alleen maar meer personeel in dienst hebben. Met dus een nauwkeuriger resultaat. De medewerkers hebben ruimte gekregen voor ander werk, bijvoorbeeld om voor een betere nabewerking te zorgen, waardoor het eindresultaat een betere kwaliteit heeft.”
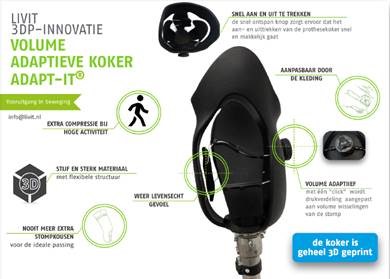
Proefkonijn
“Toen ik in dienst kwam, werkte Jan van de Werken hier nog als directeur. Hij was een hele actieve fietser en hiker, met een prothese. Hij was zo een grote inspiratie voor mij, hij liet zich nergens door tegenhouden. Daarom wilde ik, voordat hij met pensioen ging, een adaptieve prothese ontwikkelen. En dat is gelukt! Want een stomp kan door bijvoorbeeld meer en minder vocht vast te houden, van dag tot dag, of zelfs van moment op de dag, een andere pasvorm van de prothese vragen. De adaptieve prothese kan zich aanpassen aan de vorm, met een speciaal ontwikkeld mechanisme. En dat is nu een groot succes gebleken!”
De adaptieve prothese bevindt zich op dit moment nog in de testfase. “We werken nu met testklanten om een evidence based onderbouwing te maken. Dan kunnen we hem bij TNO aanbieden voor de keuring en dan is het prototype-af. Dan kunnen we veel sneller een nieuwe prothese maken, waar we nu zes dagen aan het tekenen zijn zal dat straks binnen twee uurtjes gebeurd zijn.”
Het verschil zit in de techniek
Bart begon zelf jaren geleden met FDM-printen op de zolderkamer van een vriend. “Best een gedoe ook met al die dampen”, lacht hij. “Met SLS krijg je een veel betere stevigheid, dat is echt een groot verschil. De printers van Parts on Demand zijn heel nauwkeurig en Neil zit echt aan de top als het gaat om de nieuwste materialen en nabewerkingen. We werken samen met zeven verschillende bedrijven, maar als het gaat om de adaptieve prothese, dan bestellen we die alleen bij Parts on Demand. De kwaliteit die we voor een specifiek product zoeken, bepaalt bij wie we het bestellen.”
Hij gebruikt een soort matrix om te kijken wanneer 3D-printen geschikt is. Is het rendabel, levert het meerwaarde en is het een USP. En met 3D-printen heb je geen beperkingen in je ontwerp. Dat is ook niet te onderschatten.
Voordelen van centralisatie
In maart 2020 betrok Livit een prachtig nieuw pand in Dordrecht, waar ook alle productie plaatsvindt, voor alle vestigingen in het land. “Hier konden we de centralisatie van de productie realiseren. Dat heeft enorm veel voordelen, want we wisselen hier ook de kennis en ervaring van de medewerkers uit. Het nieuwe pand van het sluitstuk van de ontwikkeling, zowel op centralisatie als op automatisering. Wij zijn erg dankbaar dat we kunnen werken met de instelling dat helpen boven winst gaat. Er wordt veel waarde gehecht aan het sociale belang dat we als bedrijf hebben. En vanwege dat sociale belang willen we ook alle technologie zelf in huis hebben. Dicht bij de patiënten. Want ieder product is iedere keer weer uniek. We hebben hier in huis een flink aantal spreekkamers en kunnen een scan maken en soms al binnen een dag de nieuwe voorziening klaar hebben. Snel reageren en helpen, daar draait het om.”
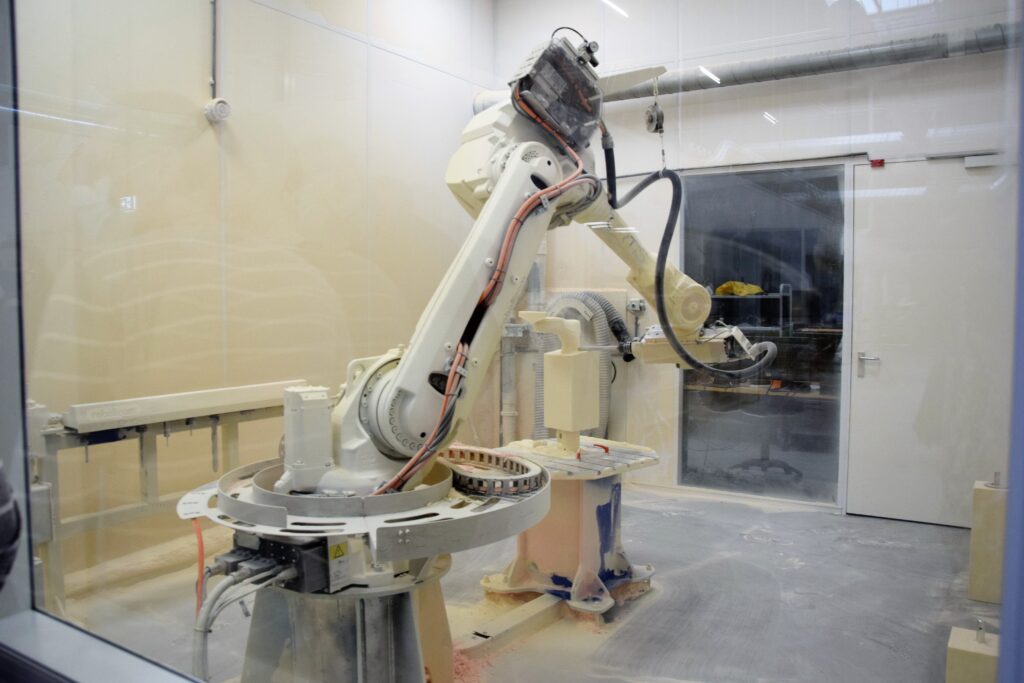
Dat sociale belang en dat helpen, dat zie je op verschillende vlakken terug, waaronder ook in het feit dat de medewerkers zelf zeer betrokken zijn bij de doelgroep. We zagen al de directeur met een prothese, maar ook een van de adviseurs is zelf al van kind af aan klant. Ook wordt er gewerkt met verschillende manieren waarop de medewerkers zelf ervaren hoe het is om een prothese te gebruiken. Zodat ze zich optimaal kunnen inleven. “We werken bijvoorbeeld ook met virtual reality en kunnen zo met mensen over de hele wereld afspreken en vergaderen. En ondanks dat protheses onze business zijn, werken we het liefst aan voorzieningen die protheses niet nodig maken.”
Waarom Parts on Demand
“De afwerking ten opzichte van de concurrenten is heel goed, en de toleranties heel nauwkeurig. We hebben een heel fijn contact waarbij er heel goed met ons meegedacht wordt. We testen met hen het nieuwste van het nieuwste.”
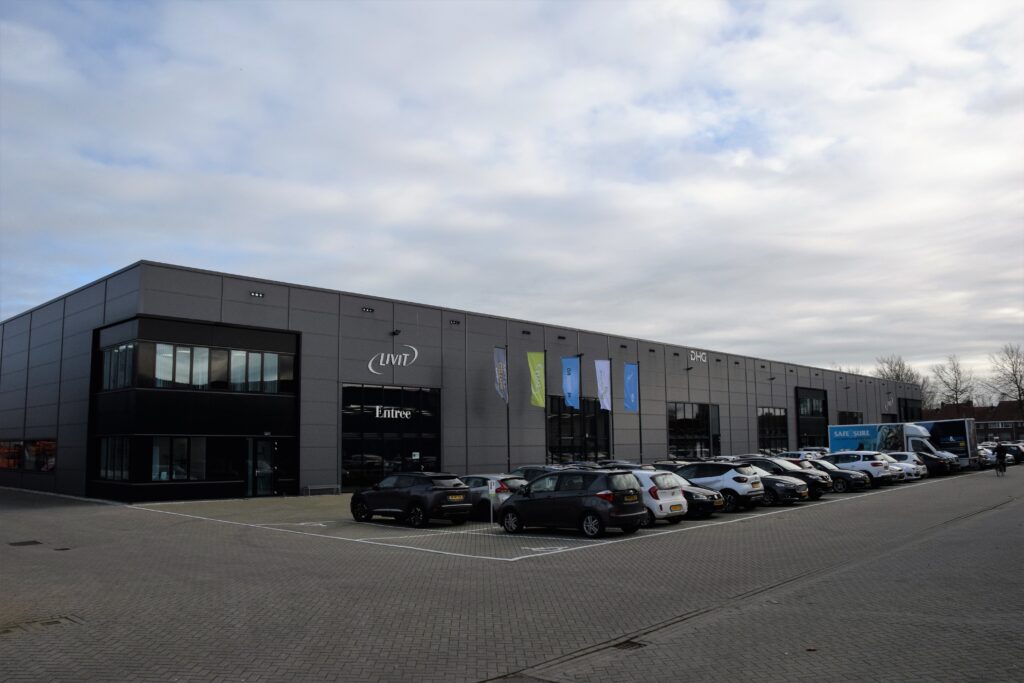
Livit
Livit ontwikkelde zich tot marktleider op het gebied van orthopedische hulpmiddelen. HAL Investments kondigde op 9 februari jongstleden de overname aan door Ottobock, die “hiermee zijn positie versterkt met internationale kennis, ervaring en innovatiekracht.”